Expert Q&A: The Designers
Interview by Jim Favret, Construction Coordinator and Amy Nelson, Leaf Litter Editor
Tell us about your experience with design-build projects for nature-based solutions.
Bryan: I have been working on design-build projects for about seven or eight years. About 95% of them have been stormwater and low-impact development retrofits to treat runoff within the public right of way. I have also worked on design-build projects involving nature-based shoreline restoration.
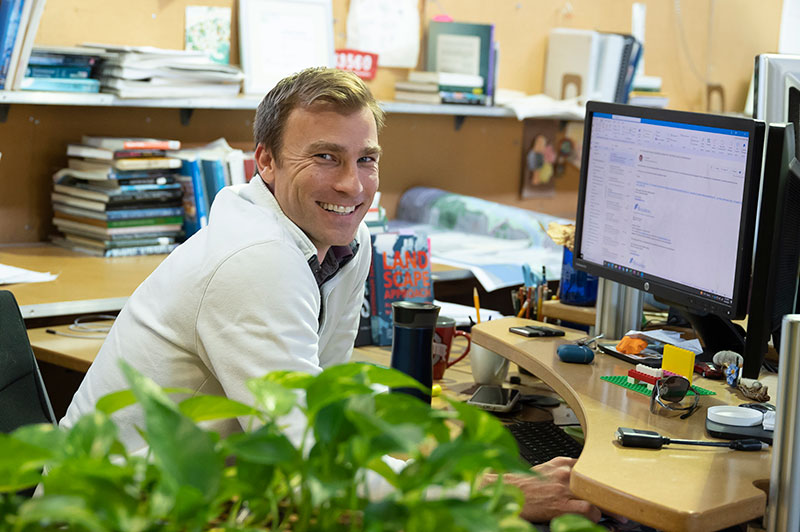
Suzanne: The first design-build project I was involved with was in 2010 in Ohio. I’ve been involved in design-build projects in the Mid-Atlantic region and the Midwest, mostly stream and wetland restoration. I have also done some design-build projects involving regenerative stormwater conveyance.
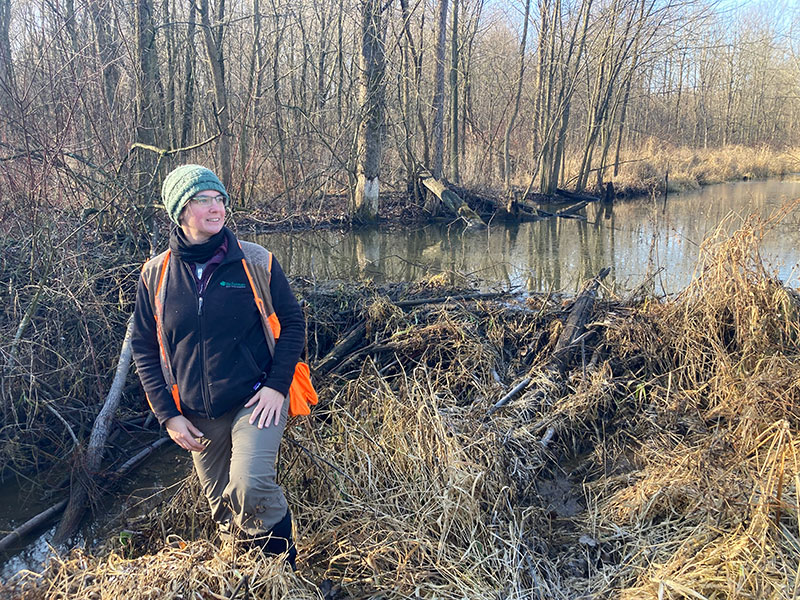
Kevin: I’ve been working on design-build projects since 2010 as well. We have completed 24 design-build projects In the Great Lakes and the Ohio River basin since 2010, and we have another eight in various stages of design and construction right now. Before the inception of the H2Ohio program in 2019, most of this design-build work was stream restoration, but since H2Ohio came on board, the bulk has been projects where we are converting agriculture to wetlands along large, contributing rivers to the Great Lakes, specifically Lake Erie.
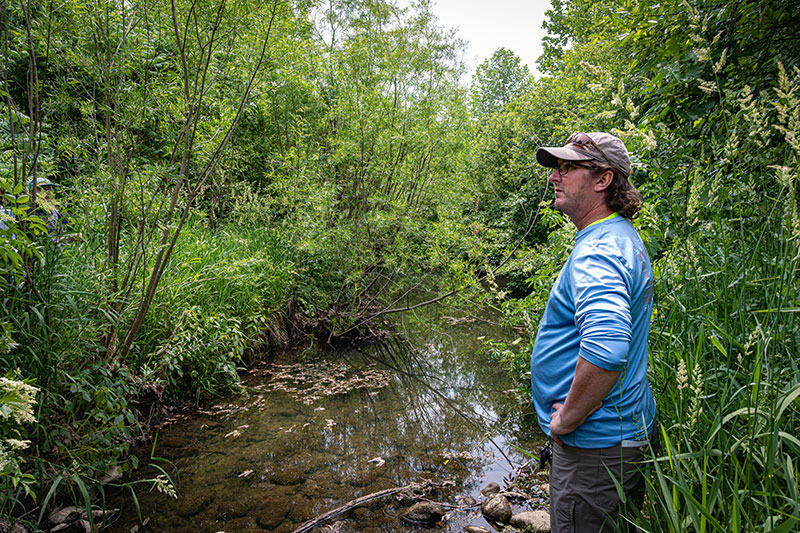
You have all worked on both design-build and design-bid-build projects. Which project delivery method do you prefer and what is the primary reason for your preference?
Bryan: I definitely prefer design-build. It provides much more flexibility—for the design itself but also for engagement with the contractor. This flexibility allows the designer to have some control over what’s being installed during construction, and the contractor to have more control during design to ensure constructability, efficiency, and high quality. There have been many occasions during design-build projects where a contractor has suggested something—whether it’s a different product or material or an alternative solution—that we’ve been able to implement in design or during construction. Design-build enables us to coordinate with contractors and solve problems much faster than we can with design-bid-build. Many of my projects are in very urban settings in the District of Columbia, where unmapped, abandoned utilities are often discovered during construction. We first have to identify whether they are actually abandoned and then determine if we can remove or work around them. That process is significantly faster with design-build.
Suzanne: I echo most of what Bryan has said. With design-build, you can adjust directly in the field without having to communicate with the contractor through the client in the form of a change order or Request For Information (RFI). Also, in putting the design together with a contractor involved from the beginning, detailed specifications are not required. It really reduces your design costs.
Kevin: I definitely prefer design-build. All of my design-build projects have been with the same contractor, so we have a great working relationship and history. We are integrating them as far back as the proposal phase, so they are vested in the project from the beginning. I just can’t say enough about the relationship that we have with that contractor.
Does your process as a designer differ when it’s design-build versus design-bid-build?
Bryan: It depends on the contractor. I’ve done design-build work with a number of contractors and there are certainly some who are more engaged in the design process. With the best design-build teams, we have been able to get that contractor involved as early on as site selection to help identify opportunities, and those contractors often have really great ideas. I don’t like working in a silo; I prefer engaging with a team. Having a contractor who has much more experience with the construction of these projects than I do, and who brings creative solutions, does change the design process in a good way. I also think it shortens the process a bit because there is also no hard cutoff between design and construction, so you can begin construction with less refined and finalized plans.
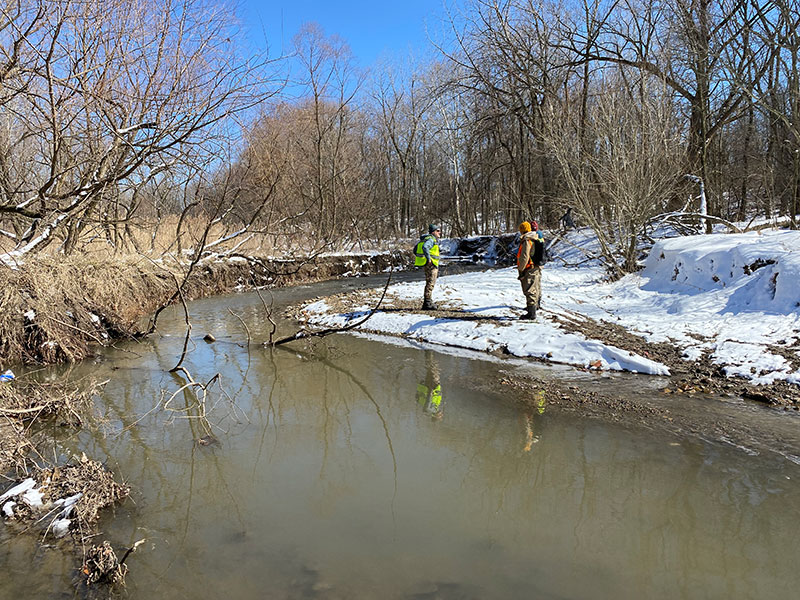
Suzanne: I think having the contractor involved also allows more creativity. They have seen the site, and we know they understand what we’re building together. There is constant communication, so you can call the contractor and be like, “Hey, I’m thinking about doing this, what are your thoughts about that?” You can get constructability questions answered by someone who knows what they’re doing, rather than trying to guess how a contractor might install something.
In the Great Lakes, a lot of our projects are grant-funded and have finite budgets. With design-build, design starts taking place during the proposal process. We have to ask, “Can we do this project and meet the goals presented in the RFP for this budget?” That collaboration continues throughout the project because you’re constantly working towards a dollar amount. Whereas with a design-bid-build project, the contractor may look at the engineer’s cost estimate and say the estimate is really off and the project can’t be built as designed.
According to the clients and contractors that we’ve interviewed for the issue, one of the most valued benefits of design-build seems to be the open communication that it affords (not just between the designer and the contractor, but also the client) and the benefits that can be associated with that. Would you guys agree?
Bryan: Absolutely. Time and cost savings are two of those benefits. And it’s not just in the project itself, but the time and overhead costs associated with the bidding process and managing two different contracts. I’ve been a part of design-bid-build projects where the bidding process has added six months or more between the end of designs and getting a permit plan set and the start of construction. That is time and money that clients don’t typically like to take. With most of our design-build projects, when we pull our permits and the designs are done and approved, construction starts within a month.
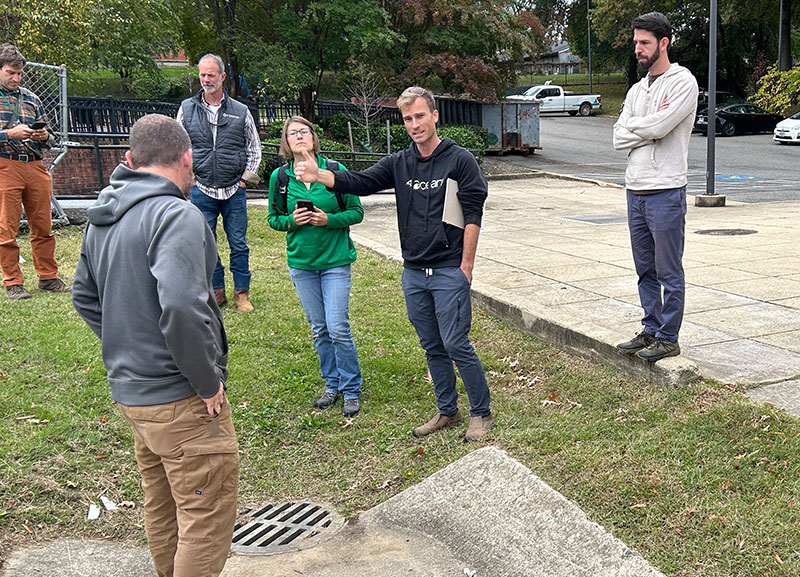
Can you share some examples of how the open communication associated with design-build has really made a difference in a project?
Bryan: Something that often gets overlooked in design-bid-build projects is site access and staging. One of the first RFIs or change orders that gets put in typically has something to do with that. I learned early on in the design-build process that it is well worth it to engage the contractor on that specific item early and make sure they have a say in how much space they need to do the construction.
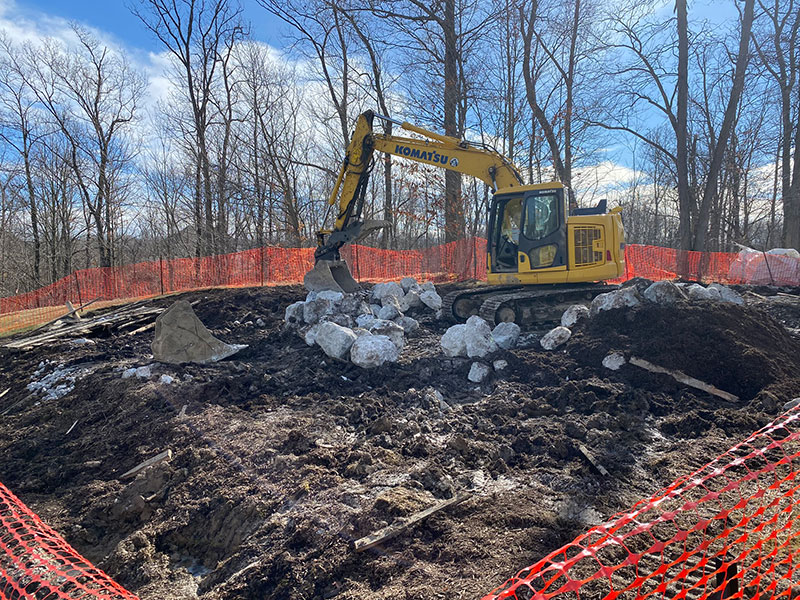
Suzanne: A lot of times what I’ve seen from a design perspective is, as we’re going through the process, being able to work with a contractor, again back to the fixed budget, if we can come up with efficiencies and extra money becomes available, the client may have an idea like adding an amphitheater for students, extra plantings, or a stream crossing, and we can collaborate with the contractor to work it in, sometimes even during the construction process. With a design-bid-build project, that would be a change order during the construction process.

Kevin: I think back to the first engineered log complex we built. The technique was new to everybody, even the contractor. We started to struggle a little bit. So, we all paused and got together to work out the best way to get the structure built. By integrating the experience of our contractor, we figured that out and got it done.
One thing we’ve heard is that design-build is advantageous when it comes to stakeholder and community engagement and support, in that the contractor becomes known and ideally trusted by the community long before construction begins. Have any of you seen this to be true?
Kevin: We recently completed a project for a city that has another project coming up, and they specifically mentioned us and the contractor as the team they want to do the design-build project.
Suzanne: I have seen a contractor become so well-known and liked in a community that the neighbors were giving them pickled asparagus from their gardens.
That’s quite a nod of approval. Tell us more.
Suzanne: Our team was recommended to the landowner by the state regulator, the contractor built a great relationship with the surrounding neighbors, as evidenced by the sharing of pickled vegetables. The landowner also let the construction crew stay in their Airbnb, which was on the property. They were able to take that savings and put it into the project for more restoration.
Bryan: Most of my design-build projects are smaller in scale, so I wouldn’t say it’s a “long” time before construction begins. The beauty of it, though, is that we can have our 90% design at a public meeting and then we might start construction a month later. We don’t have a six-month period where we’re building rapport with the community, but it does help that we can introduce the contractor to them sooner to start building that trust. I do think that there is some value in that. Is it this massive amount of trust long beforehand? I don’t know, but I think it’s nice to have that connection and touch point before construction starts.
It might not be an Airbnb and pickled asparagus situation, but it’s better than some unknown entity coming into a community with large machinery and starting to dig things up.
Bryan: Yeah. I don’t think we’ve had anyone offer their home to anyone yet.
Bryan noted earlier that design-build gives you the ability to leverage the knowledge and experience of the construction contractor while you’re designing. Can you share an example of a situation where this made a difference in one of your projects?
Bryan: I’ll share an example that may seem small, but cost-wise, it had a dramatic impact. For one of our restoration projects, we were placing post and wattle structures in some eroded gullies. This involved driving in posts across a gully and placing wattles (branches intertwined to create a dense log) between them. Our plans called for 18-inch wattles. That size had proven effective on a prior project, so that was our basis. Our contractor came back with a cost estimate for those structures that was something crazy. I don’t recall the exact amount, but it was something like five times what we had expected.
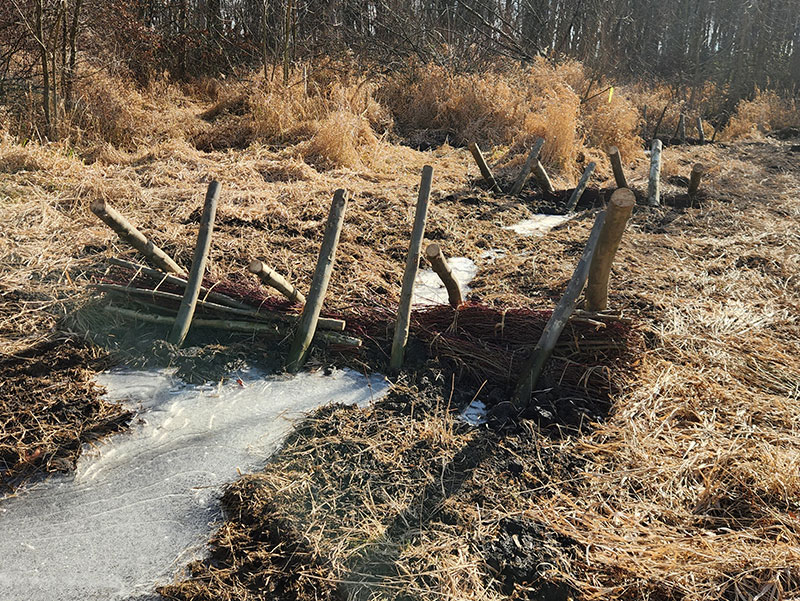
Because this was a design-build project, we were able to have a discussion with the contractor at 60% design. They told us that they could no longer get 18-inch wattles, so they had costed out using multiple smaller wattles and the manual labor time to intertwine them to make them 18 inches. They said, “If these wattles can be nine or 12 inches, it’ll be a fifth of the cost.” We all agreed that would work. This sounds silly, but had that project not been design-build, the client might have ended up spending significantly more money because that was going to be the only way the contractor would’ve been able to come up with that material. It is an example I always look back to when I think about the value of having the contractor’s input early on.
Suzanne: We had a project where the client wanted to restore a stream that flowed through a pond after dewatering. The dam had a road across the top of it, so it would be left in place with a larger culvert at the new invert installed to allow flow through. The restoration approach proposed in the RFP was going to cost more than their budget allowed. When we started talking to the contractor, we realized we could restore that part of the stream with the pond sediment in place, rather than taking all the sediment out to get down to the new culvert and then putting a drop structure in at the bottom. Coming up with this solution required figuring out if the contractor could work on the ponded sediment with their machinery, if it was feasible with the hydraulics, and if there was a way for them to access that part of the site without sinking. By working together with the contractor, we came up with a proposal that met the client’s restoration goals…and budget.
Are there any potential downsides to having the contractor at the design table?
Bryan: I would say the only thing I can think of, would be if it’s not a good team. We’ve been lucky—and I probably speak for Suzanne and Kevin here —in that we’ve been able to be selective when it comes to teaming with contractors. It’s typically people we know and have a really good rapport with. But if there is some contention, or if the team doesn’t see eye-to-eye on how things need to move forward and can’t work well together, then certainly, that could derail and delay a lot of the design and construction process.
What do you consider to be the biggest advantage that design-build brings to projects involving nature-based solutions?
Kevin: I think it’s ultimately quality. I’m thinking of a past design-bid-build stream restoration project that went to the low bidder. The contractor had never done a stream restoration project before, and it was a disaster. The client basically said, “Well, this is the best we’re going to be able to do.” I just think of how much better the end result would have been if the project had been design-build.
Are there any disadvantages to design-build?
Bryan: One reason that some people may not go the design-build route is funding. A lot of this work is grant-funded. The client only has funding for design, and they might need to have that design to pursue funding for the construction. If funders offered more opportunities for design-build work, I believe we’d see a lot more of it.
So, one disadvantage is that it is not always an option. In some states and municipalities, procurement policies can also be a barrier.
Suzanne: I was recently talking to a fellow designer from another firm who really would like to do design-build. They approached their employer about it, and although their employer was interested in the idea, they said they couldn’t do it because of liability and risk. With designer-led design-build, an engineering firm is accepting a lot of risk. A contractor, on the other hand, can take out bonding and insurance to cover the risk, because they do that regularly.
How is your role as a designer on a design-build project different from your role as a designer on a design-bid-build project where part of the scope includes construction oversight? What value does the designer bring to the construction site on a design-build project?
Bryan: In a design-bid-build project where we are providing construction oversight, we are not technically giving the contractor direction. We are not liable at that point. If we make any recommendations, they have to go through the client or construction management company for approval. With my design-build projects (which have always been designer-led, by the way) I can work directly with the contractor to find a solution. We might have to get approval from an inspector or regulator or the client if there is a very significant change to the design, but even when that is the case, we can get through that process quickly with design-build. Most of the time, changes can be made without change orders on design-build projects. With design-bid-build projects even little changes typically require change order requests to the client.
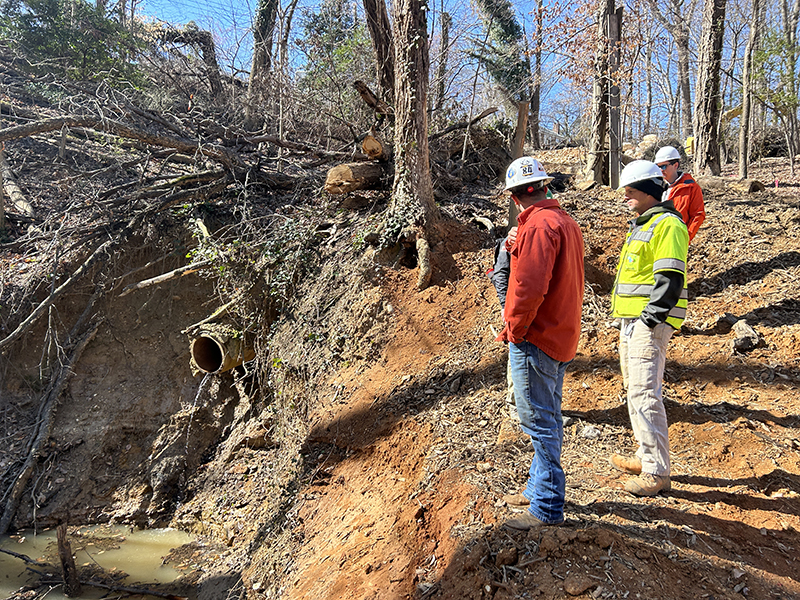
Suzanne: When you’re doing construction oversight for a design-bid-build project, you’re noting down your observations, but you can’t really say anything that defers from the design plans. On a design-build project, you can say, “Hey, can you put more brush here or make the slope of this flatter than the plans are showing?” and not have to worry about change orders, delays, and approvals.
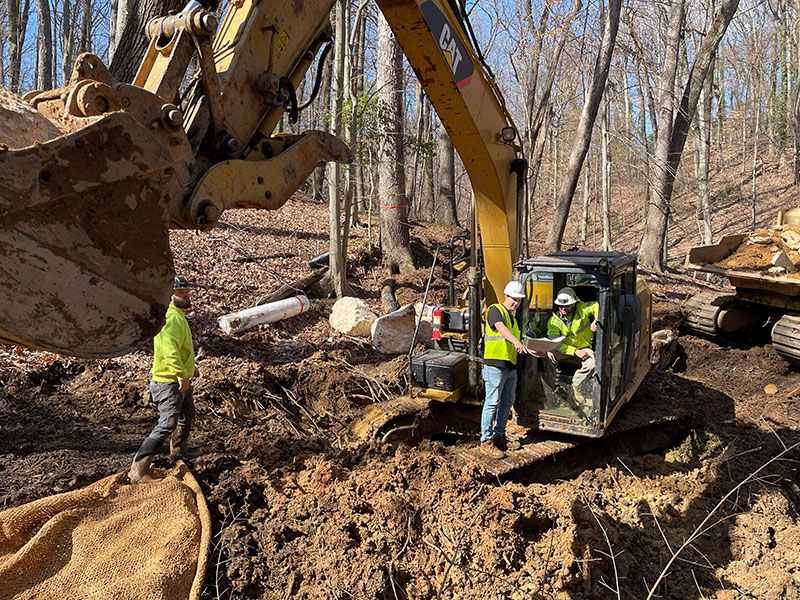
Kevin: Often for design-bid-build projects, our construction oversight role is relatively minor. It may be just be a construction kickoff meeting, a visit or two, and then a plan-in-hand or a punch list meeting. When we’re doing design-build, we’re on site multiple times a week throughout the duration of the project.
Have you noticed a difference in client satisfaction with design-build projects vs. design-bid-build?
Bryan: The one thing I can say is that I know that we have had repeat business, that they’ve been very happy, and that this approach allows them to concentrate on doing more projects.
We know you feel a sense of ownership and accountability with all of your work, but is it any stronger or different with design-build compared to design-bid-build?
Bryan: I’ll definitely say for me, yes. I think most engineers want to get their hands dirty too, and it’s nice to be able to go out to the construction site and work with the contractor to make sure that the finished product is really what you had envisioned during the design process. With design-bid-build, you can’t really guide the contractor or provide explanations for some details or some part of the design plans. That requires a lengthier RFI process. I do feel a bit more of a sense of accomplishment with design-build projects than I do with projects where I have just done the design package.

Kevin: Tt’s definitely more meaningful working on design-build projects. I feel like I’m designing and building projects with my friends. We’re constantly revisiting past projects. Our contractor just asked me the other day for a photo from a past project. We have a shared history, as opposed to a design-bid-build project, where it might be the only time we ever work with a contractor and never see them again.
It seems like that team mentality is intrinsic to design-build, and that you all feel pretty fortunate to be working on design-build projects. But not everyone is using design-build. What’s one thing you would tell a client who currently uses the design-bid-build delivery method but is considering design-build (assuming they can, given their funding sources and procurement regulations)?
Suzanne: Design-build will not only decrease your headaches; it will enable you to put more money back into your project.
What about a peer from another design firm who may be reluctant to try the design-build approach because of their perception of the risk involved? What would you say to them?
Suzanne: I’d suggest that they read this issue of Leaf Litter because it might answer their questions.
Bryan: We paint a rosy picture here, but we do a lot of designer-led design-build projects, so there is a lot more risk put on us. I don’t think it’s something that should be entered into lightly. We’ve had success and we’ve built enough experience and work with certain teams to make sure that we all understand what we agree to when we put in a proposal for a design-build project. One of the key factors is making sure that you know your team ahead of time and that you select the contractors and subcontractors you know you can work with well because in a design-build project, you’re kind of married to them.
According to the Design-Build Institute of America, design-build is the most popular and fastest-growing delivery method for all U.S. construction projects. But design-build for nature-based solutions is relatively new. Do you think the design-build approach is having any kind of impact on the practice?
Bryan: Our clients are extremely busy, and they are typically understaffed and overworked. Design-build has allowed us to take more off our clients’ shoulders and help them get more projects done. So, it certainly allows us to do more.